Housekeeping facility
Top sales list housekeeping facility

Port Elizabeth (Eastern Cape)
Job Position: Business Unit / Operations Manager (automotive related industry) Ref: 3640 Location: Port Elizabeth Salary: R55 000 to R60 000 per month CTC commensurate with experience and qualification Qualifications / Requirements Degree / Diploma in Production Management / Engineering Strong middle management person who can take strong control of the departments Business unit experience highly advantageous Experience in authority of making decisions Hands on team management with clear goal setting and project mapping / management with the team Sound knowledge of Good Manufacturing Practices (GMP) Sound understanding of quality standards Minimum of 8 year’s experience in an automotive manufacturing environment of which 5 years need to be in a supervisory role (stable work record) which include Operations Strong communication skills and professional disposition Impeccable work ethics and integrity Strong leadership skills and ability to motivate and drive, teams Key Performance Areas: Handling of all round operations Customer negotiations, presentations and visits Handling of key customers Managing of staff (operationally) Daily production: Run daily production meetings Ensure daily production reports are completed and handed in Analyse any deviations to planned versus actual production numbers Create plan to rectify any deviations from planned production numbers Daily resource plan for absenteeism deviations for production staff Ensure production plan is aligned to available stock and make changes accordingly, ensure sales are aware of changes Decide on when over time is required to meet production targets Ensure returns are checked and findings reported to senior management Intra-day updates to sales on production status Plant maintenance: Ensure maintenance on plant and equipment is completed in accordance to maintenance schedule Tools usage report Personnel: Decide on the number of factory staff needed based on production targets using time study information from IE Department Weekly meetings with staff to inform and motivate Update and maintain the manufacturing performance board Quality, Health and Safety Health and safety: Ensure health and safety procedures and protocols are followed throughout the company Quality manual: Ensure the manual is up to date and matches the quality procedures within production Corrective action reports: Manage the opening and closing of any corrective action reports created by the quality department Facility management: Ensure internal housekeeping is maintained in the plant and adheres to the quality manual Ensure internal and external aspects of the facility are in working order (security, tanks, windows, leaks) and take necessary action Induction training: Ensure correct induction training is done Industrial Engineering Production: Ensure all production processes are up to date Create and present production improvement concepts for management for both factory expansion and efficiency improvement. Layouts: Manage implementation of any new processes and procedures Ensure factory Layouts are up to date Equipment: Provide motivations for new equipment purchases Ensure maintenance schedule is update and relevant Responsibility: Salary: R55 000 to R60 000 per month CTC commensurate with experience and qualification Qualifications / Requirements Degree / Diploma in Production Management / Engineering Strong middle management person who can take strong control of the departments Business unit experience highly advantageous Experience in authority of making decisions Hands on team management with clear goal setting and project mapping / management with the team Sound knowledge of Good Manufacturing Practices (GMP) Sound understanding of quality standards Minimum of 8 year’s experience in an automotive manufacturing environment of which 5 years need to be in a supervisory role (stable work record) which include Operations Strong communication skills and professional disposition Impeccable work ethics and integrity Strong leadership skills and ability to motivate and drive, teams Key Performance Areas: Handling of all round operations Customer negotiations, presentations and visits Handling of key customers Managing of staff (operationally) Daily production: Run daily production meetings Ensure daily production reports are completed and handed in Analyse any deviations to planned versus actual production numbers Create plan to rectify any deviations from planned production numbers Daily resource plan for absenteeism deviations for production staff Ensure production plan is aligned to available stock and make changes accordingly, ensure sales are aware of changes Decide on when over time is required to meet production targets Ensure returns are checked and findings reported to senior management Intra-day updates to sales on production status Plant maintenance: Ensure maintenance on plant and equipment is completed in accordance to maintenance schedule Tools usage report Personnel: Decide on the number of factory staff needed based on production targets using time study information from IE Department Weekly meetings with staff to inform and motivate Update and maintain the manufacturing performance board Quality, Health and Safety Health and safety: Ensure health and safety procedures and protocols are followed throughout the company Quality manual: Ensure the manual is up to date and matches the quality procedures within production Corrective action reports: Manage the opening and closing of any corrective action reports created by the quality department Facility management: Ensure internal housekeeping is maintained in the plant and adheres to the quality manual Ensure internal and external aspects of the facility are in working order (security, tanks, windows, leaks) and take necessary action Induction training: Ensure correct induction training is done Industrial Engineering Production: Ensure all production processes are up to date Create and present production improvement concepts for management for both factory expansion and efficiency improvement. Layouts: Manage implementation of any new processes and procedures Ensure factory Layouts are up to date Equipment: Provide motivations for new equipment purchases Ensure maintenance schedule is update and relevant Salary: R55000 to 60000 Job Reference #: Business Unit - Operations Manager - automotive re
See product

Port Elizabeth (Eastern Cape)
Job Position: Business Unit - Operations Manager - automotive related industry Ref: 3640 Location: Port Elizabeth Salary: R55 000 to R60 000 per month CTC commensurate with experience and qualification Qualifications / Requirements • Degree / Diploma in Production Management / Engineering • Strong middle management person who can take strong control of the departments • Business unit experience highly advantageous • Experience in authority of making decisions • Hands on team management with clear goal setting and project mapping / management with the team • Sound knowledge of Good Manufacturing Practices (GMP) • Sound understanding of quality standards • Minimum of 8 year’s experience in an automotive manufacturing environment of which 5 years need to be in a supervisory role (stable work record) which include Operations • Strong communication skills and professional disposition • Impeccable work ethics and integrity • Strong leadership skills and ability to motivate and drive, teams Key Performance Areas: • Handling of all round operations • Customer negotiations, presentations and visits • Handling of key customers • Managing of staff (operationally) • Daily production: o Run daily production meetings o Ensure daily production reports are completed and handed in o Analyse any deviations to planned versus actual production numbers o Create plan to rectify any deviations from planned production numbers o Daily resource plan for absenteeism deviations for production staff o Ensure production plan is aligned to available stock and make changes accordingly, ensure sales are aware of changes o Decide on when over time is required to meet production targets o Ensure returns are checked and findings reported to senior management o Intra-day updates to sales on production status • Plant maintenance: o Ensure maintenance on plant and equipment is completed in accordance to maintenance schedule o Tools usage report • Personnel: o Decide on the number of factory staff needed based on production targets using time study information from IE Department o Weekly meetings with staff to inform and motivate o Update and maintain the manufacturing performance board o Quality, Health and Safety • Health and safety: o Ensure health and safety procedures and protocols are followed throughout the company • Quality manual: o Ensure the manual is up to date and matches the quality procedures within production • Corrective action reports: o Manage the opening and closing of any corrective action reports created by the quality department • Facility management: o Ensure internal housekeeping is maintained in the plant and adheres to the quality manual o Ensure internal and external aspects of the facility are in working order (security, tanks, windows, leaks) and take necessary action • Induction training: o Ensure correct induction training is done Industrial Engineering • Production: o Ensure all production processes are up to date o Create and present production improvement concepts for management for both factory expansion and efficiency improvement. • Layouts: o Manage implementation of any new processes and procedures o Ensure factory Layouts are up to date • Equipment: o Provide motivations for new equipment purchases o Ensure maintenance schedule is update and relevant Responsibility: Qualifications / Requirements • Degree / Diploma in Production Management / Engineering • Strong middle management person who can take strong control of the departments • Business unit experience highly advantageous • Experience in authority of making decisions • Hands on team management with clear goal setting and project mapping / management with the team • Sound knowledge of Good Manufacturing Practices (GMP) • Sound understanding of quality standards • Minimum of 8 year’s experience in an automotive manufacturing environment of which 5 years need to be in a supervisory role (stable work record) which include Operations • Strong communication skills and professional disposition • Impeccable work ethics and integrity • Strong leadership skills and ability to motivate and drive, teams Key Performance Areas: • Handling of all round operations • Customer negotiations, presentations and visits • Handling of key customers • Managing of staff (operationally) • Daily production: o Run daily production meetings o Ensure daily production reports are completed and handed in o Analyse any deviations to planned versus actual production numbers o Create plan to rectify any deviations from planned production numbers o Daily resource plan for absenteeism deviations for production staff o Ensure production plan is aligned to available stock and make changes accordingly, ensure sales are aware of changes o Decide on when over time is required to meet production targets o Ensure returns are checked and findings reported to senior management o Intra-day updates to sales on production status • Plant maintenance: o Ensure maintenance on plant and equipment is completed in accordance to maintenance schedule o Tools usage report • Personnel: o Decide on the number of factory staff needed based on production targets using time study information from IE Department o Weekly meetings with staff to inform and motivate o Update and maintain the manufacturing performance board o Quality, Health and Safety • Health and safety: o Ensure health and safety procedures and protocols are followed throughout the company • Quality manual: o Ensure the manual is up to date and matches the quality procedures within production • Corrective action reports: o Manage the opening and closing of any corrective action reports created by the quality department • Facility management: o Ensure internal housekeeping is maintained in the plant and adheres to the quality manual o Ensure internal and external aspects of the facility are in working order (security, tanks, windows, leaks) and take necessary action • Induction training: o Ensure correct induction training is done Industrial Engineering • Production: o Ensure all production processes are up to date o Create and present production improvement concepts for management for both factory expansion and efficiency improvement. • Layouts: o Manage implementation of any new processes and procedures o Ensure factory Layouts are up to date • Equipment: o Provide motivations for new equipment purchases o Ensure maintenance schedule is update and relevant Salary: R55000 to 60000 Job Reference #: Business Unit - Operations Manager - automotive re
See product
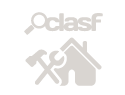
South Africa
Job Purpose Manage Project Activities Responsibilities and Duties · Attend Production/Site meetings and understand the project’s and the customer’s requirements. · Assign tasks and targets to Team Leaders and Personnel in close coordination with the Project Managers (subject to the workload, project requirements and company requirements). · Plan and prioritize production activities and allocate personnel accordingly for ongoing and upcoming projects in close coordination with the Project Managers to meet deadlines of ongoing projects. · Follow-up on the production activity, maintaining and updating production task list · Continual monitoring of progress, conduct time studies and improve efficiency for production related processes identifying any shortcomings and possible problems. · Management of project related equipment lay out within facility. · Monitor the presence of all the production personnel and prepare daily timesheets along with assignment of personnel to the on-going projects. · Manage shift pattern in an efficient and economic manner after prior consultation with the project manager. · Responsible for discipline of production personnel and bringing to the attention and action of management any illegal, unsafe, unprofessional and irresponsible activities. · Supervise the servicing, maintenance and repair of facility equipment. · Make recommendations for equipment upgrades, improvements and optimizing. · Monitor, consumables and equipment receipts ordering, proper accounting and storage. · Relay production related requirements to project store for incoming parts and issuance of parts · Determine special tooling requirement for upcoming project. · Ensure that personnel are informed on the technical, quality and safety requirements for the tasks they have been tasked to perform. · Advise Management of training requirements and skills levels of production personnel. · Take responsibility and accountability for the safety and the general housekeeping in the facility. · Daily tasking of safety officer for safety related mater pertaining to production activities. · Verify, store, maintain, control, supervise and be responsible for customer’s property. · Assist with the assessment, mentoring, training, counseling and motivation of production personnel. · Responsible to familiarize yourself and promote and enforce as far as possible the company quality, safety and environmental policies and procedures. · Identify and advise management on personnel, facility and equipment requirements. Identify shortcomings and make recommendations for continuous improvements. PERSON SPECIFICATION Position Project Supervisor Experience · Qualified Tradesman with at least 5 years’ experience · Supervisor Experience in piping/site work. Qualification and Knowledge / Requirements · Obtaining your criminal record is a condition of employment · Will require Police Clearance Certificate For more information, please email a comprehensive cv to
See product

Port Elizabeth (Eastern Cape)
Job Position: Manufacturing Operations Manager Ref: 3640 Location: Port Elizabeth Salary: R45 000 to R55 000 per month CTC commensurate with experience and qualification Qualifications / Requirements • Degree / Diploma in Production Management / Engineering • Sound knowledge of Good Manufacturing Practices (GMP) • Sound understanding of quality standards • Minimum of 8 year’s experience in an automotive manufacturing environment of which 5 years need to be in a supervisory role (stable work record) which include Operations • Strong communication skills and professional disposition • Impeccable work ethics and integrity • Strong leadership skills and ability to motivate and drive, teams Key Performance Areas: • Handling of all round operations • Customer negotiations, presentations and visits • Handling of key customers • Managing of staff (operationally) • Daily production: o Run daily production meetings o Ensure daily production reports are completed and handed in o Analyse any deviations to planned versus actual production numbers o Create plan to rectify any deviations from planned production numbers o Daily resource plan for absenteeism deviations for production staff o Ensure production plan is aligned to available stock and make changes accordingly, ensure sales are aware of changes o Decide on when over time is required to meet production targets o Ensure returns are checked and findings reported to senior management o Intra-day updates to sales on production status • Plant maintenance: o Ensure maintenance on plant and equipment is completed in accordance to maintenance schedule o Tools usage report • Personnel: o Decide on the number of factory staff needed based on production targets using time study information from IE Department o Weekly meetings with staff to inform and motivate o Update and maintain the manufacturing performance board o Quality, Health and Safety • Health and safety: o Ensure health and safety procedures and protocols are followed throughout the company • Quality manual: o Ensure the manual is up to date and matches the quality procedures within production • Corrective action reports: o Manage the opening and closing of any corrective action reports created by the quality department • Facility management: o Ensure internal housekeeping is maintained in the plant and adheres to the quality manual o Ensure internal and external aspects of the facility are in working order (security, tanks, windows, leaks) and take necessary action • Induction training: o Ensure correct induction training is done Industrial Engineering • Production: o Ensure all production processes are up to date o Create and present production improvement concepts for management for both factory expansion and efficiency improvement. • Layouts: o Manage implementation of any new processes and procedures o Ensure factory Layouts are up to date • Equipment: o Provide motivations for new equipment purchases o Ensure maintenance schedule is update and relevant Salary: R45000 to 50000 Job Reference #: Manufacturing Operations Manager
See product
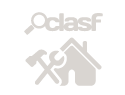
South Africa
LOCATION Gauteng - Johannesburg - Kempton Park OVERVIEW The successful applicant will be required to oversee and ensure the integrity and movement of the inventory, stores and stock keeping facilities and processes of the company. MINIMUM REQUIREMENTS · Minimum of 5 years experience overseeing/managing an engineering and/or earthmoving storing facility. · Must have Grade 12 (Matric). · Must have an Accounting / Bookkeeping / Inventory Control / Warehousing & Logistics Diploma / Certificate. · Sound knowledge of engineering/earthmoving inventory categories and control. · Advanced Computer Skills & Literacy. · Experience in systems like GP and Citrix beneficial. · Currently holds a supervisory or management experience. · Extremely strong communications skills. · Ability to manage relationship with customers, suppliers, fellow employees, subordinates and management. · Strong ability to address and resolve queries / problems efficiently and effectively. · Team work orientated, proactive and meticulous. · Hands on individual willing to accept accountability and responsibility. · Extreme attention to detail and adherence to procedures. KEY RESPONSIBILITIES · Planning, leading, organizing and controlling all activities related to stock / inventory control and movement. · Oversee the 8 – 10 employees and plan their tasks and duties effectively and conduct other related duties. · Ensuring the accuracy and integrity of the stock levels and system. · Ensure that stock levels are kept at expected levels. · Maintain ethical and professional relationships with suppliers and other internal departments. · Ensure reporting to done accurately and efficiently as and when required. · Ensure clerical and admin duties are performed and kept up to date. · Be aware of production/stock needs and requirements of the different departments/sites in the organisation. · Ensure Health and Safety standards are met and maintained. · Manage cycle and year-end stock counts. DUTIES will include but are not limited to tasking and supervision of the following areas: · Monitor stock availability and levels. · Arrange and procure stock and other relevant consumables where required. · Plan for and execute stock counts accurately and efficiently. · Ensure security measures are kept pertaining to stock. · Sign off obsolete and stock write offs. · Housekeeping. · Ensure accuracy in dispatching and receiving stock (includes stock received from site). · Monitor and report on diesel levels. · Ensure access control procedures are met and the system is working. · Arrange and oversee the loading and offloading of vehicles. ADMINISTRATION · Recording of hours worked by employees and other HR related duties pertaining to this position. · Updating of stock sheets and that sound stock taking principals are maintained and followed throughout the organisation. · Ensure actual stock versus system integrity by updating stock movement and location on the relevant system. · Ad hoc administrative duties as required by management. · Ensuring that month end reports relating to areas of responsibilities from sites meet deadlines. · Liaise with relevant departments in order to identify needs and plan accordingly. SALARY / BENEFITS · Market related packages which includes the following: o Subsidised Medical Aid o Pension Scheme o Death, Disability and funeral cover o 13th Cheque o Incentive Scheme Bonus Salary: +_ R Cost to company EMAIL CV
See product
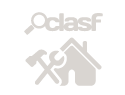
East London (Eastern Cape)
Job Overview: Seeking an experienced Shift supervisor to manage and coordinate the efforts of hourly department employees to meet manufacturing and production schedules. To ensure that product specifications are met with a high standard of quality. To ensure compliance with all standards, policies, regulations, for the safe, environmentally sound production of a quality product. Minimum Requirements: Grade 12 National Diploma in Production Supervisor / Management Recognised Apprenticeship in Converting / Corrugator preferable 3+ Years of experience working in a manufacturing, production environment 2+ Years of experience supervising employees within a manufacturing, production environment Availability to work shift work and overtime when needed Knowledge of ISO9001, ISO14001, ISO45001, ISO22001 Experience with computer applications such as Microsoft Office (Word, Excel, and Outlook) Responsibilities: Work closely with team members to provide a safe work environment Make recommendations to improve safety, environmental and health of the entire facility Responsible for the day-to-day operations of the shift with constant emphasis on safety, quality, delivery, and cost Plan, assign and direct work for all hourly production employees; appraise performance and provide feedback as needed Assist in resolving complaints; hold employees accountable as needed; communicate issues and results daily Responsible to maintain department visual controls, and continuous improvement methods to the manufacturing floor Direct and execute daily production requirements Meet or exceed productivity goals Maintain waste generation at or below budgeted standard Inspect the finished product to ensure quality specifications are met Maintain full compliance with all policies; safety rules; housekeeping excellence Ensure all production reporting is completed timely and accurately for each shift Ability to recognize the importance of safety in the workplace, follow safety rules, utilise appropriate safety equipment and report unsafe conditions to the appropriate administrator Building effective teams to support continuous improvement Conduct constructive production and safety meetings Competencies/Skills: Problem solving/root cause analysis skills Leadership and interpersonal skills Ability to motivate teams to exceed expectations Communication Planning and organizations skills Sense of urgency and accountability Customer focus Ability to work effectively in cross functional team environment
See product