Manufacturing plant
Top sales list manufacturing plant

Nylstroom (Limpopo)
Complete inline palasade manufacturing plant. Coil holder, bender and shaper, cutter and collector.
R 70.000
See product

Ermelo (Mpumalanga)
Plant Fitters (x 2), Ermelo, Rneg + Ben Grade 12 Trade test as Fitter (Olifantsfontein – Section 28) 5 years exp as Fitter in plant/ Manufacturing concern (Agri &/ Forestry) Strong fitting ability Knowledge of hydraulic and pneumatic systems Basic welding Excellent communication skills Ability to work independently in a team environment DUTIES To Do Maintenance And Breakdown Repairs On All Mechanical Equipment To Perform Inline Inspections. Reports Any Difficulties Or Faults Arising In The Operation Or Utilization Of The Equipment Maintain OHASA Standards And Ensure High Levels Housekeeping. Adhere To All Health & Safety Regulations
See product

East London (Eastern Cape)
Plant AccountantPlant Accountant (Automotive) required for a large automotive company based in East London.Responsibilities: Ensure the correct level of stock is held for the business requirements.Review and approval of purchase price, BOM and standard costs changes.Understand and maintain standard costing for existing parts.Control and report all plant launch costs.Full responsibility for specific P&L lines.Ensure that all HSE policies and procedures are adhered to at all times.To be able to prepare VAT and EMP 201.Requirements:BCom Accounting Degree/ Diploma or equivalent/CIMAAccounting Experience working in Manufacturing with ERP experience of standard cost and BOMUnderstanding of IATF16949 / ISO9001AS400 (System21) or similar operating system.Hyperion experienceExperience of SOX Internal Audit proceduresQADShould you wish to apply please email your CV through to Kerry O’Hagan at Kerry@profilepersonnel.co.zaOnly shortlisted candidates will be contacted. Should you not receive a response within 14 days please consider your application unsuccessful. We will keep your CV on our database for any other relevant roles that may arise.
See product

East London (Eastern Cape)
Responsibilities Process development (process flow chart) for functions Use industrial engineering methods to determine the Cycle times Manufacture feasibility analysis (DFA/DFM) and PFMEA on new products Plant and process layout for new products and plant launches and new technology implementation Perform Process and quality improvements in functional areas Digitizing process, converting hard patterns into electronic format using digitizing hardware and software. Configuration and nesting process for cutting setup on Lectra equipment and software Perform cost analysis of product and process alternatives (investments and assembly time, cutting yield) Write process specifications and make recommendations regarding ergonomic improvements Write specifications for manufacturing equipment and make recommendations for equipment procurement Simulate continuous improvement process in plants (KAIZEN, DO IT) with the objective of MEQ Work with SD-Teams to complete product launches Monitor and improve 4 M’s of a stable of production Stimulate TPM in new projects Monitor and audit manufacturing best practices and standards in the plant Improvement strategies: Participate and/or lead activities for manufacturing footprint analysis, continuous improvement of new and/or ongoing manufacturing process, and lean manufacturing implementation Will be required to work shifts and/or OT if required Requirements:• National Diploma or Degree in Engineering (mechanical or industrial), or equivalent experience• 3-4 years minimum experience as a Manufacturing or Process Engineer advantage if in cutting technology• OEM or Tier One automotive interiors work experience• High volume automotive manufacturing engineering work experience• Strong computer and manufacturing simulation skills, Lectra and Optitex software packages relevant to cutting• Strong Technical background in mechanical and/or Industrial Engineering• Proven track record working with Cutting and Sewing machinery• Manufacturing exposure in Automotive Industry• Plant Layout using AUTO CAD• Equipment selection, purchasing, and installation
See product

Port Elizabeth (Eastern Cape)
Job Position: Manufacturing Operations Manager Ref: 3640 Location: Port Elizabeth Salary: R45 000 to R55 000 per month CTC commensurate with experience and qualification Qualifications / Requirements • Degree / Diploma in Production Management / Engineering • Sound knowledge of Good Manufacturing Practices (GMP) • Sound understanding of quality standards • Minimum of 8 year’s experience in an automotive manufacturing environment of which 5 years need to be in a supervisory role (stable work record) which include Operations • Strong communication skills and professional disposition • Impeccable work ethics and integrity • Strong leadership skills and ability to motivate and drive, teams Key Performance Areas: • Handling of all round operations • Customer negotiations, presentations and visits • Handling of key customers • Managing of staff (operationally) • Daily production: o Run daily production meetings o Ensure daily production reports are completed and handed in o Analyse any deviations to planned versus actual production numbers o Create plan to rectify any deviations from planned production numbers o Daily resource plan for absenteeism deviations for production staff o Ensure production plan is aligned to available stock and make changes accordingly, ensure sales are aware of changes o Decide on when over time is required to meet production targets o Ensure returns are checked and findings reported to senior management o Intra-day updates to sales on production status • Plant maintenance: o Ensure maintenance on plant and equipment is completed in accordance to maintenance schedule o Tools usage report • Personnel: o Decide on the number of factory staff needed based on production targets using time study information from IE Department o Weekly meetings with staff to inform and motivate o Update and maintain the manufacturing performance board o Quality, Health and Safety • Health and safety: o Ensure health and safety procedures and protocols are followed throughout the company • Quality manual: o Ensure the manual is up to date and matches the quality procedures within production • Corrective action reports: o Manage the opening and closing of any corrective action reports created by the quality department • Facility management: o Ensure internal housekeeping is maintained in the plant and adheres to the quality manual o Ensure internal and external aspects of the facility are in working order (security, tanks, windows, leaks) and take necessary action • Induction training: o Ensure correct induction training is done Industrial Engineering • Production: o Ensure all production processes are up to date o Create and present production improvement concepts for management for both factory expansion and efficiency improvement. • Layouts: o Manage implementation of any new processes and procedures o Ensure factory Layouts are up to date • Equipment: o Provide motivations for new equipment purchases o Ensure maintenance schedule is update and relevant Salary: R45000 to 50000 Job Reference #: Manufacturing Operations Manager
See product

South Africa (All cities)
We are acclaimed leaders in manufacturing, fabricating and supplying hospital oxygen plants, which are used for producing oxygen for application in industrial applications. We are known all over the globe for building plant machinery in compliance with international standards. Our clients are satisfied with the performance and quality of our medical oxygen generator plant. We have been given ISO 9001:2008 and CE certifications. Applications of Medical Oxygen Plant:- * Biotechnology * Pharmaceutical * First-aid and Emergencies * Chemical Scope and Supply Our Products:- * Medical Oxygen Generator Plant * Medical Gas Filling Plant * Medical Oxygen Production Plant * PSA Medical Oxygen Plant Visit website: www.medicaloxygenplant.com Call: (+91) 9818255334 R-19 Hauz Khas Enclave, Delhi - 110016 India If you have further questions please don't hesitate to call us.
Free
See product

Uitenhage (Eastern Cape)
Our client, a leader in the automotive sector, seeks to employ a Manufacturing Production Technician to join their Production department. Position based in Uitenhage/Kariega. Duties: Apply statistical methods and perform mathematical calculations to determine manufacturing processes, staff requirements and production standards. Coordinate quality control objectives and activities to resolve production problems, maximise product reliability and minimise costs. Confer with vendors, staff and management personnel regarding purchases, procedures, product specifications, manufacturing capabilities and project status. Draft and design layout of equipment, materials and workspace to illustrate maximum efficiency. Review production schedules, engineering specifications, orders and related information to obtain knowledge of manufacturing methods, procedures and activities. Communicate with management and user personnel to develop production and design standards. Estimate production costs and effect of product design changes for management review, action and control. Study operations sequence, material flow, functional statements, organisation charts and project information to determine worker functions and responsibility. Evaluate precision and accuracy of production and testing equipment and engineering drawings to formulate corrective action plan. Analyse statistical data and product specifications to determine standards and establish quality and reliability objectives of finished product. Develop manufacturing methods, labour utilisation of standards and cost analysis systems to promote efficient staff and facility utilisation. Recommend methods for improving utilisation of personnel, material and utilities. Plan and establish sequence of operations to fabricate and assemble parts or products and promote efficient utilisation. Complete production reports, purchase requisitions and material, tool and equipment list. Lead and coach an analytical approach to problem solving. Inspect and monitor work areas, examine tools and equipment and provide employee safety training to prevent, detect, and correct unsafe working conditions or violations of procedures or safety rules. Manage and lead team members, programmers when required/assigned. Requirements: Industrial/Mechanical Engineering diploma At least 2 years' automotive industrial engineering experience Must have experience in mechanical installation and maintenance work on plant electrical systems and equipment Broad knowledge of controls and mechanisms Proficient in troubleshooting, design and optimisation of systems Proficient in work combinations table Job Reference #: PE004381/CT
See product
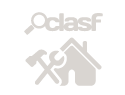
Port Elizabeth (Eastern Cape)
Production Manager – Food Manufacturing (FMCG) We’re looking to appoint a hands-on and proactive Production Manager in a growing Food Manufacturing company based in Port Elizabeth. The ideal candidate will require to meet the following: Requirements: Applicable Tertiary Qualification in Production Management or / BTech (Engineering) or BSc Engineering or similar. Minimum of 7 years of similar management experience in the production of Food or Pharma or other quality regulated industry environment. Excellent management and leadership skills. Self-motivated and able to work independently. Strong critical thinking, problem-solving and analytical skills. Quality and compliance-focused. Ability to interact professionally with multiple departments to effectively meet customer requirements. Planning and Organisational Skills. Good understanding of Kaizen and lean manufacturing principles. Excellent verbal and written communication skills. Good interpersonal skills. Ability to coach and mentor subordinates. Ability to handle disciplinary matters. Report writing skills. Proficiency in MS Office applications and understanding of MRP’s. Ability to handle multiple tasks. Willingness to work long hours as required. Ability to manage a variety of cross-functional team members Responsibilities: Daily production planning, monitoring and meeting customer targets. Oversee the production process at the plant. Maintain and build integrated working relationships with all departments. Managing production staff and relevant human resources matter to ensure operational effectiveness. Continue to build a collaborative and positive workplace for all. Other applicable tasks within the scope of the role. Ensure adherence to quality control standards, food safety requirements (FSSC). Stock management and efficient utilisation of resources. Manage department personal hygiene code of conduct. Ensure compliance with national standards and legislation. Oversee departmental administration and record keeping. Investigate and address complaints. Manage and evaluate machine resources to ensure productivity and minimum downtown. Ensure that products are produced on time, at the required company quality standards, cost effectively and meeting customer requirements. Analyse budgets and continuously control production costs. Identify training needs and ensure that proper training is provided for all production staff. Develop employees to meet the future requirements of the company. Promote continuous improvements within the production function. Please send CV to info@naxosbaking.co.za
See product

South Africa (All cities)
BuildMate is a strong technology-oriented, high-tech engineering project and execution company providing technology and supply of machinery and equipment for building material projects. If you are looking for top-tier AAC block plant machinery manufacturers in Hyderabad, India, then look no further. Buildmate is the best AAC block manufacturing unit supplier in India that is committed to delivering premium-quality AAC block plants at competitive prices. If you are worried about the maintenance of the AAC block plant, these manufacturers provide customized solutions that cater to the specific needs of the customer.
See product

South Africa (All cities)
We are manufacturers and suppliers of nitrogen plant in India. The best quality materials and components are used in the fabricating in compliance with the best manufacturing practices. We manufacture nitrogen plants with the latest advanced cryogenic distillation technology in different sizes and capacities ranging from 20m3/hour to 1000m3/hour at the best prices in the market. Complete compliance with quality control has enabled us to get ISO 9008:2015 and CE certifications. Scope of Supply of Nitrogen Gas Generators: * Air Compressor * Refrigerant Dryer with Filter * Buffer Tank * Oxygen Generator * Oxygen Buffer Tank * Outlet Features of Nitrogen Generators: * Full Automation * Fast Start-up * Very Advanced * High Performing * High Reliability * Molecular Sieves Life Company Details: Website: http://www.nitrogenplants.com Email: info@nitrogenplants.com Mobile: +91 9810626301 Address: Hauz Khas Enclave, Delhi, 110016 India Give us a quick call and get your order to us today!!
R 4.541.750
See product

Allanridge (Free State)
"Fenton Technologies Pvt. Ltd. is a professional Engineering equipment’s Manufacturing and Environmental research and development, production and sales of science and technology enterprises. Since its inception, we always adhere to the spirit of craftsmanship, to provide the industry with water treatment equipment and services and systematic solutions, Company Work in Three Verticals- Sewage Water Projects , Wastewater Products, Swimming Pools Products include MBR Membrane , Oil Skimmer, Screw Press, MBR STP Plant, Bar Screen, Dissolved Air Flotation (DAF) many More water treatment Equipment’s . Fenton is also Associating with Overseas partners to Keep in Forefront . Our Water Treatment Equipment Company always welcome innovation & Advance Technologies Developers for Association in Market . In product quality improvement, the water treatment equipment company “customer first” philosophy for the development, adhering to the “quality, innovation and service” business purposes, the establishment of a set of international standards of quality assurance management system."
See product

South Africa (All cities)
Fenton Technologies Pvt. Ltd. is a distinguished science and technology enterprise specializing in equipment professional engineering manufacturing, environmental research and development. Committed to craftsmanship since inception, we provide innovative water treatment solutions across three verticals: Sewage Water Projects, Wastewater, and Swimming Pool Products. Our offerings encompass MBR Membranes, Oil Skimmers, Screw Presses, MBR STP Plants, Bar Screens, and Dissolved Air Flotation units. Collaborating with international partners, we remain at the forefront of advancements. We welcome pioneering developers to join our quest for innovation and contribute to the market’s progress.
See product
2 photos

Paarl (Western Cape)
EE Candidates Only Food Manufacturing Plant seeks a Food Technologist to do reviews on existing product effectiveness with a view to modifications and improvements in order to maintain competitiveness in the market place. Develop new products to meet identified market needs and supply the marketing department with technical information for use in new product evaluation. OUTPUTS: Attend product exhibitions & consumer focus groups Implement product development plan Conduct new raw material & product feasibility studies Assist & document quality & technical processes and design & maintain product specifications & labels Manage team and assist resolution of customer complaints MINIMUM EXPERIENCE: 7 years relevant experience A senior Food Technologist with prerequisite experience and knowledge of wheat flour processing and quality, yeast leavened applications, processes and related ingredient technology/functionality. MINIMUM QUALIFICATIONS: Relevant National Diploma Email your CV to anthonyjobs@wcp.co.za
See product
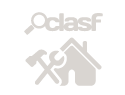
East London (Eastern Cape)
Machine Operators needed for a manufacturing plant based in East London Must have matric and Machine Operator experience Salary R40 per hour excluding overtime. Must be willing to work shifts
See product

Uitenhage (Eastern Cape)
REQUIREMENTS Perform corrective, preventative and predictive maintenance work according to Company and Industry standard Active participation in projects focused on improvements of machinery and processes Adhere to all health, safety and environment standards and ensure that work is carried out in a safe manner at all times Perform assigned programming tasks Generate the necessary documentation associated with this work and participate in the work of training maintenance personnel and sharing acquired knowledge, whenever required to do so Document anomalies, generate work reports and general status reports of the work assigned daily Request the material resources necessary for the correct performance of the planned maintenance Decides and acts independently in the absence of superiors with regards to the incidents and repairs of the company machines and installations Ad hoc duties as required Qualification/Skills/Experience Required Minimum Electrical /Mechanical Engineering qualification, B-Tech preferred Minimum 5 years Siemens S7 experience, TIA portal, Profibus, WinCC. Allen Bradley will be advantageous. Minimum- 5 years’ experience within a high production demand automotive manufacturing plant Excellent computer knowledge and skills. Fault finding and problem solving. Teamplayer Ideally someone from a system integration background. Willing to work rotating shifts, flexible hours, weekends and during shutdown, if/when required.
See product

Port Elizabeth (Eastern Cape)
Job Position: Business Unit / Operations Manager (automotive related industry) Ref: 3640 Location: Port Elizabeth Salary: R55 000 to R60 000 per month CTC commensurate with experience and qualification Qualifications / Requirements Degree / Diploma in Production Management / Engineering Strong middle management person who can take strong control of the departments Business unit experience highly advantageous Experience in authority of making decisions Hands on team management with clear goal setting and project mapping / management with the team Sound knowledge of Good Manufacturing Practices (GMP) Sound understanding of quality standards Minimum of 8 year’s experience in an automotive manufacturing environment of which 5 years need to be in a supervisory role (stable work record) which include Operations Strong communication skills and professional disposition Impeccable work ethics and integrity Strong leadership skills and ability to motivate and drive, teams Key Performance Areas: Handling of all round operations Customer negotiations, presentations and visits Handling of key customers Managing of staff (operationally) Daily production: Run daily production meetings Ensure daily production reports are completed and handed in Analyse any deviations to planned versus actual production numbers Create plan to rectify any deviations from planned production numbers Daily resource plan for absenteeism deviations for production staff Ensure production plan is aligned to available stock and make changes accordingly, ensure sales are aware of changes Decide on when over time is required to meet production targets Ensure returns are checked and findings reported to senior management Intra-day updates to sales on production status Plant maintenance: Ensure maintenance on plant and equipment is completed in accordance to maintenance schedule Tools usage report Personnel: Decide on the number of factory staff needed based on production targets using time study information from IE Department Weekly meetings with staff to inform and motivate Update and maintain the manufacturing performance board Quality, Health and Safety Health and safety: Ensure health and safety procedures and protocols are followed throughout the company Quality manual: Ensure the manual is up to date and matches the quality procedures within production Corrective action reports: Manage the opening and closing of any corrective action reports created by the quality department Facility management: Ensure internal housekeeping is maintained in the plant and adheres to the quality manual Ensure internal and external aspects of the facility are in working order (security, tanks, windows, leaks) and take necessary action Induction training: Ensure correct induction training is done Industrial Engineering Production: Ensure all production processes are up to date Create and present production improvement concepts for management for both factory expansion and efficiency improvement. Layouts: Manage implementation of any new processes and procedures Ensure factory Layouts are up to date Equipment: Provide motivations for new equipment purchases Ensure maintenance schedule is update and relevant Responsibility: Salary: R55 000 to R60 000 per month CTC commensurate with experience and qualification Qualifications / Requirements Degree / Diploma in Production Management / Engineering Strong middle management person who can take strong control of the departments Business unit experience highly advantageous Experience in authority of making decisions Hands on team management with clear goal setting and project mapping / management with the team Sound knowledge of Good Manufacturing Practices (GMP) Sound understanding of quality standards Minimum of 8 year’s experience in an automotive manufacturing environment of which 5 years need to be in a supervisory role (stable work record) which include Operations Strong communication skills and professional disposition Impeccable work ethics and integrity Strong leadership skills and ability to motivate and drive, teams Key Performance Areas: Handling of all round operations Customer negotiations, presentations and visits Handling of key customers Managing of staff (operationally) Daily production: Run daily production meetings Ensure daily production reports are completed and handed in Analyse any deviations to planned versus actual production numbers Create plan to rectify any deviations from planned production numbers Daily resource plan for absenteeism deviations for production staff Ensure production plan is aligned to available stock and make changes accordingly, ensure sales are aware of changes Decide on when over time is required to meet production targets Ensure returns are checked and findings reported to senior management Intra-day updates to sales on production status Plant maintenance: Ensure maintenance on plant and equipment is completed in accordance to maintenance schedule Tools usage report Personnel: Decide on the number of factory staff needed based on production targets using time study information from IE Department Weekly meetings with staff to inform and motivate Update and maintain the manufacturing performance board Quality, Health and Safety Health and safety: Ensure health and safety procedures and protocols are followed throughout the company Quality manual: Ensure the manual is up to date and matches the quality procedures within production Corrective action reports: Manage the opening and closing of any corrective action reports created by the quality department Facility management: Ensure internal housekeeping is maintained in the plant and adheres to the quality manual Ensure internal and external aspects of the facility are in working order (security, tanks, windows, leaks) and take necessary action Induction training: Ensure correct induction training is done Industrial Engineering Production: Ensure all production processes are up to date Create and present production improvement concepts for management for both factory expansion and efficiency improvement. Layouts: Manage implementation of any new processes and procedures Ensure factory Layouts are up to date Equipment: Provide motivations for new equipment purchases Ensure maintenance schedule is update and relevant Salary: R55000 to 60000 Job Reference #: Business Unit - Operations Manager - automotive re
See product

Port Elizabeth (Eastern Cape)
Job Position: Business Unit - Operations Manager - automotive related industry Ref: 3640 Location: Port Elizabeth Salary: R55 000 to R60 000 per month CTC commensurate with experience and qualification Qualifications / Requirements • Degree / Diploma in Production Management / Engineering • Strong middle management person who can take strong control of the departments • Business unit experience highly advantageous • Experience in authority of making decisions • Hands on team management with clear goal setting and project mapping / management with the team • Sound knowledge of Good Manufacturing Practices (GMP) • Sound understanding of quality standards • Minimum of 8 year’s experience in an automotive manufacturing environment of which 5 years need to be in a supervisory role (stable work record) which include Operations • Strong communication skills and professional disposition • Impeccable work ethics and integrity • Strong leadership skills and ability to motivate and drive, teams Key Performance Areas: • Handling of all round operations • Customer negotiations, presentations and visits • Handling of key customers • Managing of staff (operationally) • Daily production: o Run daily production meetings o Ensure daily production reports are completed and handed in o Analyse any deviations to planned versus actual production numbers o Create plan to rectify any deviations from planned production numbers o Daily resource plan for absenteeism deviations for production staff o Ensure production plan is aligned to available stock and make changes accordingly, ensure sales are aware of changes o Decide on when over time is required to meet production targets o Ensure returns are checked and findings reported to senior management o Intra-day updates to sales on production status • Plant maintenance: o Ensure maintenance on plant and equipment is completed in accordance to maintenance schedule o Tools usage report • Personnel: o Decide on the number of factory staff needed based on production targets using time study information from IE Department o Weekly meetings with staff to inform and motivate o Update and maintain the manufacturing performance board o Quality, Health and Safety • Health and safety: o Ensure health and safety procedures and protocols are followed throughout the company • Quality manual: o Ensure the manual is up to date and matches the quality procedures within production • Corrective action reports: o Manage the opening and closing of any corrective action reports created by the quality department • Facility management: o Ensure internal housekeeping is maintained in the plant and adheres to the quality manual o Ensure internal and external aspects of the facility are in working order (security, tanks, windows, leaks) and take necessary action • Induction training: o Ensure correct induction training is done Industrial Engineering • Production: o Ensure all production processes are up to date o Create and present production improvement concepts for management for both factory expansion and efficiency improvement. • Layouts: o Manage implementation of any new processes and procedures o Ensure factory Layouts are up to date • Equipment: o Provide motivations for new equipment purchases o Ensure maintenance schedule is update and relevant Responsibility: Qualifications / Requirements • Degree / Diploma in Production Management / Engineering • Strong middle management person who can take strong control of the departments • Business unit experience highly advantageous • Experience in authority of making decisions • Hands on team management with clear goal setting and project mapping / management with the team • Sound knowledge of Good Manufacturing Practices (GMP) • Sound understanding of quality standards • Minimum of 8 year’s experience in an automotive manufacturing environment of which 5 years need to be in a supervisory role (stable work record) which include Operations • Strong communication skills and professional disposition • Impeccable work ethics and integrity • Strong leadership skills and ability to motivate and drive, teams Key Performance Areas: • Handling of all round operations • Customer negotiations, presentations and visits • Handling of key customers • Managing of staff (operationally) • Daily production: o Run daily production meetings o Ensure daily production reports are completed and handed in o Analyse any deviations to planned versus actual production numbers o Create plan to rectify any deviations from planned production numbers o Daily resource plan for absenteeism deviations for production staff o Ensure production plan is aligned to available stock and make changes accordingly, ensure sales are aware of changes o Decide on when over time is required to meet production targets o Ensure returns are checked and findings reported to senior management o Intra-day updates to sales on production status • Plant maintenance: o Ensure maintenance on plant and equipment is completed in accordance to maintenance schedule o Tools usage report • Personnel: o Decide on the number of factory staff needed based on production targets using time study information from IE Department o Weekly meetings with staff to inform and motivate o Update and maintain the manufacturing performance board o Quality, Health and Safety • Health and safety: o Ensure health and safety procedures and protocols are followed throughout the company • Quality manual: o Ensure the manual is up to date and matches the quality procedures within production • Corrective action reports: o Manage the opening and closing of any corrective action reports created by the quality department • Facility management: o Ensure internal housekeeping is maintained in the plant and adheres to the quality manual o Ensure internal and external aspects of the facility are in working order (security, tanks, windows, leaks) and take necessary action • Induction training: o Ensure correct induction training is done Industrial Engineering • Production: o Ensure all production processes are up to date o Create and present production improvement concepts for management for both factory expansion and efficiency improvement. • Layouts: o Manage implementation of any new processes and procedures o Ensure factory Layouts are up to date • Equipment: o Provide motivations for new equipment purchases o Ensure maintenance schedule is update and relevant Salary: R55000 to 60000 Job Reference #: Business Unit - Operations Manager - automotive re
See product

East London (Eastern Cape)
Job Position: Qualified Fitter and Turner Ref: 3585 Location: Berlin (outside East London) Salary: R25 000 per month commensurate with experience + Provident and Medical Aid Qualifications / Requirements: • Educational: - Grade 12 (Matric) Senior certificate. - Qualified Artisan i.e. Fitter and Turner / Millwright (Trade Tested) - Computer literacy - fair level of experience with MS Office - Windows - Supervisor/Leadership training • Additional courses / experience (added advantage): - First Aid - Level 1 or 2 - Fire Fighting - Basic or Fire Marshal - Health and Safety Representative - Computer Training (PPT, Excel, Word, etc) - Strong maintenance related knowledge and principles - Supervisory/management experience • Purpose of function: - To ensure that the manufacturing processes run effectively and efficiently to produce economical products that meet specified quality standards and specifications - Fully responsible for all operational and plant maintenance, together with the associated quality control within the production environments • Key Performance Areas: - Supervisory role in Maintenance/Workshop department - Maintenance of plant, machinery and equipment - Manufacturing/machining of parts - Order/monitor spare parts and consumables - Safety, Health & Environment (SHE) • Proven experience in the maintenance field, within a manufacturing environment • The position would require “leadership / supervision”, but still very much requires a “hands-on” approach in the working environment • The candidate must be comfortable with the workplace location (Berlin), and for providing a remote support service, for a 5 to 6 day working week Responsibility: Qualifications / Requirements: • Educational: - Grade 12 (Matric) Senior certificate. - Qualified Artisan i.e. Fitter and Turner / Millwright (Trade Tested) - Computer literacy - fair level of experience with MS Office - Windows - Supervisor/Leadership training • Additional courses / experience (added advantage): - First Aid - Level 1 or 2 - Fire Fighting - Basic or Fire Marshal - Health and Safety Representative - Computer Training (PPT, Excel, Word, etc) - Strong maintenance related knowledge and principles - Supervisory/management experience • Purpose of function: - To ensure that the manufacturing processes run effectively and efficiently to produce economical products that meet specified quality standards and specifications - Fully responsible for all operational and plant maintenance, together with the associated quality control within the production environments • Key Performance Areas: - Supervisory role in Maintenance/Workshop department - Maintenance of plant, machinery and equipment - Manufacturing/machining of parts - Order/monitor spare parts and consumables - Safety, Health & Environment (SHE) • Proven experience in the maintenance field, within a manufacturing environment • The position would require “leadership / supervision”, but still very much requires a “hands-on” approach in the working environment • The candidate must be comfortable with the workplace location (Berlin), and for providing a remote support service, for a 5 to 6 day working week Salary: R25000 Job Reference #: Qualified Fitter and Turner
See product

Bloemfontein (Free State)
KEY OUTPUTS PART OF THE PROGRAM (PROJECT BASED) Lead and coordinate Communities of Practice and Centres of Excellence as agreed Facilitate the implementation of the Manufacturing Way in South Africa Lead the Manufacturing Development Team to ensure; Strategic Alignment Shared Learning''s Best Practice Progress Reviews Work practice reviews (e.g. GEM Audits) / Assessments & verifications and the development and coordination of related improvement plans. Promote Knowledge Management processes in South Africa. Facilitate the identification and implementation manufacturing improvement projects. Facilitate, co-ordinate and lead divisional improvement projects Establish policies and standards for manufacturing services in order to ensure consistency, efficiency, integrity in the maintenance and productivity environments. Develop the one to three years plant business plan to ensure that customer service and productivity objectives are met. Manage the systematic and strategic coordination of all Manufacturing business functions as aligned with the Sales and Operational Planning process (S&OP). Manage the implementation of world class manufacturing processes across Manufacturing for the purpose of ensuring the continuous improvement of short to long-term performance. Manage the synchronisation of all aspects of Manufacturing including flow of materials and final goods. Management and maintenance of the Manufacturing assets at a productive basic condition. Measurement and monitoring of performance trends and the application of focused improvement initiatives in order to increase total system efficiency, effectiveness and reliability. Identification, development and the implementation of the relevant enablers in order to deliver the Plant business plan and budget. Develop and implement people capability enhancement plans to ensure that business improvement objectives are met. Ensure that supply chain planning is aligned to meeting customer needs. QUALIFICATIONS / EXPERIENCE BSc Engineering: Mechanical, Electrical, Industrial Engineering Minimum 5 years experience in manufacturing environment including 3 years experience in implementing supply chain, production or process improvement related initiatives. 3 Years experience as an area manager (e.g. Unit Manager, Manufacturing Excellence Manager) in an FMCG manufacturing environment Experience in leading capital or process improvement projects Demonstrable experience in people change initiatives and process improvement Membership of a professional institute would be advantageous
See product
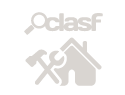
Ermelo (Mpumalanga)
INTRODUCTION A leading dynamic Animal Feed Manufacturing business in Mpumalanga, existing for more than 30 years, are looking for a factory manager. We are responsible for producing animal feed to local clients in the monogastric and ruminant fields. JOB PURPOSE Manages the various production activities through subordinates in order to achieve planned production targets and to ensure the effective use of available resources. REQUIREMENTS Relevant production qualification of animal feed plant or a mill plant. Must have at least 2 years hands on experience in feed production and or maintenance and a minimum of 2 years in a production management position with related plant managing a team of operators. Valid driver’s license, willing to relocate, between 30 and 40 years of age. Must have experience in ensuring safety, health & hygiene in a production environment. Minimum Gr12 and speaking Zulu would be advantageous. DUTIES AND RESPONSIBILITIES Leading a team that is responsible for the total production function in terms of functional responsibilities of all equipment. Aligning, guiding and co-coordinating the activities of a team to utilize the skills and experience of each team member to achieve targets in terms of production volumes, quality, uptime, safety, costs and staff development. To keep management up to date of all risk, plant, equipment, people and quality issues Accomplishes manufacturing results by communicating job expectations, planning, monitoring and appraising job results, disciplining employees, initiating, coordinating, and enforcing systems policies and procedures. Maintains workflow by monitoring steps of the process, setting processing variables, observing control points and equipment, monitoring personnel and resources, studying methods, implementing cost reductions, facilitating corrections to malfunctions, within process control points. Completes production plan by scheduling and assigning personnel, accomplishing work results, establishing priorities, monitoring progress, resolving problems, reporting results on production sheets. Maintains quality requirements by establishing and enforcing standards Maintains a safe and clean working environment, maintains compliance with established policies and procedures. Daily monitoring of actual production against the planned targets Identifying and reporting quality problems to the CEO. Taking full responsibilities for the entire plant’s functions Ensure efficient collaboration and co-ordination between all departments including maintenance, production, procurement, sales and distribution. May also need to assist the maintenance technician if required from time to time.
See product

Rustenburg (North West)
Make Hotel Soap at 25 cents - 50 cents each! Hotel soap bars are in high demand all year round. Annually, hotel guests consume tons of soaps, shower shampoos, gels, etc. Hotels are reducing plastic waste. THE DEMAND FOR HOTEL SOAP BARS and SHAMPOO BARS IS SET TO INCREASE! Join the market and become the owner of OUR ALL NEW SMALL SOAP PLANT. S.A. First. The Small Soap Plant includes 3 Pieces of Machinery and Startup raw materials: 1. Soap Mixer. 2. Soap Extruder. 3. Manual Soap Press. 4. Training Make 50kg per hour. Price Small Soap Plant: ONLY R 168 000. MANUFACTURING COST OF 15g - 30g HOTEL SOAP: 25 - 50 cents each. Sell the 15 - 30g Hotel Soap Bar at R0.80 - R1.50 each. Profit: 200% plus. Advantages of Purchasing The Small Soap Plant: Very Low Price. (The nearest imported is R1m - R1.5m plus). Locally manufactured. Very profitable business: 200%. Easy to use, safe, 3phase 1-2 employees. Small space needed. Quality supplies. Soap Noodles feedstock. Training. Support. Versatile and expansive: you can make Laundry bars, household Bath soaps, natural organic soaps USING THE SAME MACHINE. Get in touch to get started. FIRST COME. FIRST SERVED LIMITED ORDERS PER MONTH. LEAD TIME: 4 - 8 Weeks. PROSPERITY AND ABUNDANCE begins with an idea. Next is ACTION! IT'S YOUR MOVE. Technical support, training and supplies WATCH YOUR BUSINESS GROW!
R 168.000
See product

East London (Eastern Cape)
FITTER AND TURNER MINIMUM JOB REQUIREMENTS • Matric / NTC 3. • Completed trade test as Fitter and Turner with Red Seal certificate preferred or relevant equal experience. • Strong experience in the servicing or installation of: o Hydraulic and pneumatic equipment; o Boilers and steam applications; o Variable speed gear boxes; and o Overhead cranes and gantries • Proven experience as a welder. • A minimum of 5 years’ experience in a manufacturing environment. • Experience in a sawmilling environment will be preferred. • Medically fit with sober habits. • Code EB license with own transport. • Willing to work irregular hours and perform standby duties. • Available to start on short notice. • Must be able to communicate in English (speak, read & write). • Ability to communicate in Xhosa will be an added advantage. Please send detailed CV to etongoodwin@e2estaffing.co.za Responsibility: JOB DESCRIPTION • Perform cost-effective mechanical maintenance and repairs on all plant and ancillary equipment. • Cost-effective installation of new plant and machinery. • Recording of all work performed on plant and ancillary equipment on a job card. • Maintaining an up-to-date knowledge of all mechanical plant and ancillary equipment on site. • Maintain a high level of housekeeping and total compliance with safety standards within his work area. • Performing of overtime work and standby duties as and when required. • Assisting with on the job training of apprentices and semi-skilled artisans working in the engineering division. • Requisitioning of spares and materials. • Assist in the formulation and implementation of a planned maintenance program. Please send detailed CV to etongoodwin@e2estaffing.co.za Job Reference #: FITTER AND TURNER Consultant Name: Eton Goodwin
See product
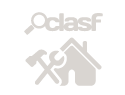
Port Elizabeth (Eastern Cape)
Batching concrete loads accurately, in line with mix designs and technical specifications Completing associated administration with regards to the batching of concrete Effective communication with Drivers and other plant staff Daily completion of order downloads and stock take Receiving raw materials and ensuring that the quality and quantity is correct Ensure general plant area is maintained and clean according to company standards Completion of general plant functions Gain experience and a general understanding of Ready-Mix operations Grade 12 (Matric) Minimum 5 years production / manufacturing / operations experience, preferably in a ready-mix environment. Ensuring that all Health and Safety rules are implemented and adhered to on site Ability to maintain professional communication with clients and staff. Management of staff allocated to site. Forward CV's to Ronel - hradmin@scribcon.co.za
See product

East London (Eastern Cape)
A East London EC manufacturing - automotive component industry requires an Experienced SETTER with PLASTICS INJECTION MOULDING expertise. Our client in the automotive component industry requires an Experienced SETTER with PLASTICS INJECTION MOULDING expertise. ROLE: SETTER Sector: Automotive Industry - Plastics Injection Moulding Location: East London, South Africa Employment Type: full Time Equity: The appointment will be made in line with the company's equity terms. Experience: 6 years Salary Package: TBA Assessment: **All shortlisted applicants will be required to undergo assessments process /testing Education: Compulsory NQF level 4 in SETTING PLASTICS INJECTION MOULDING (** Proven track record) Matric 6 years setting experience in a plastic injection moulding environment/industry DUTIES MACHINES: Start-up of machine at the beginning of the shift Attend to process problems on machines Ensure that machines are operating at optimum cycle time, consistent with quality requirements Correctly fit all water and hydraulic hoses as per setting as per setting sheet for the part/s. Set up machine and tool using the setting sheet for the part/s. Obtaining 1st off approval prior to commencement of Production. Authorising the COC for the part by way of signature. TOOLS: Setting tools in accordance with priority plan and process work instructions Assess last –off against first –off at the end of each production/tool change Report any necessary tool repair requirements to the Tool Controller Follow the daily Production Plan for the changing of tools or instruction from Planner. Installation of the tool into machine must be done within the allocated time. Placement of non-running tools in the correct area with the last off positioned on top. Carry out problem escalation procedure when M/C or tool problems occur. STAFF: Responsible for ensuring that operators understand quality requirements as per work instruction Ensure effective communication with other shifts to ensure smooth running of plant. SCRAP: Implement action plans/corrective action with regards to scrap control where necessary SAFETY - HOUSEKEEPING Ensure high level of housekeeping and plant maintenance Obey all company rules and regulations at all times, i.e. Safety, Quality, Environmental, Housekeeping etc. Attend to and resolve any non-conformances related to Quality or escalate problems. Ensure 5S activities are carried out in your working areas. APPLICATION TERMS: REF Code: 2001EL16: GKC/and or our client reserves the right to change the job specifications without notice. All application are confidential. Correspondence will only be conducted with short listed candidates. Should you not hear from us within 10 days, please consider your application unsuccessful but registered on our database for future job.
See product

Paarl (Western Cape)
Experience required: • Minimum of 3 years’ post-trade working experience in a technical steel/manufacturing environment. • Sound knowledge of maintenance and control over electrical systems in a plant. • PLC Programming skills will be highly advantageous. Skills and knowledge required: • Electrical work in a plant environment. • Panels and DB Boards. • Automated machines. • PLC’s (programming advantageous). • Drives and/or invertors. • Generator electrical systems. • Control systems. • Mains and/or reticulation. Salary: RNEG Consultant Name: Melanie Stevens
See product
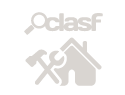
Vredefort (Free State)
Vacancy Details Employer:Grain Field Chickens Pty Ltd INTRODUCTIONGrain Field Chickens, a subsidiary of VKB Agriculture PTYLtd, is a dynamic role player in the integrated broiler industry with an abattoir in Reitz in the North Eastern Free State. We offer you the opportunity to establish yourself within a professional, corporate environment in the countryside.JOB DECRIPTIONThe HR Officer will be responsible for providing support in the various human resources functions which include IR Industrial Relations, workforce planning, AWOL & absenteeism management, recruitment, training & development and performance management & monitoring.JOB REQUIREMENTSGrade 12 or NQF Level 4 equivalent.A relevant HR Degree or Diploma from a recognized institution.At least 5 years- experience in a similar role is essential.Min 5 years IR expertise gained within the FMCG / Manufacturing/ Agriculture environment unionized environment.Solid, proven and applied understanding of the LRA and BCEA.Microsoft Office / HR Systems is essential.Very strong Excel skills on advanced level.Must be able to maintain confidentiality at all times.Ability to understand and speak the vernacular used in the Eastern Free State Southern Sotho will be a definite advantage.A clear criminal record.Drivers licence and own transport.A willingness to work overtime, incl. Saturdays, when required.JOB DESCRIPTIONHuman ResourcesContribute in and assist with drafting and executing the GFC Annual HR Plan.Assist with the development of HR SOPs, procedures and processes.Assist with the drafting and review of Job Descriptions.Assist with drafting new KPIs and reviewing exiting ones.Assist with SLAs between HR and the various internal departments.Assist with the periodic staff EOS and actioning thereof in conjunction with the plant engineer.Assist with ensuring the Succession Planning Program is kept live and current in all departments.Assist with PIP with respect to poor performance management.Together with the HR Manager, assist the onsite clinic with drawing up and driving the GFC Annual Wellness Program.Together with the systems administrator, ensure that the plant authorised Manload is kept up to accurately at all times.Conduct IR/ HR Training on a quarterly basis.Ensure accurate records are kept in line with company policy.Ensure all internal & external visitors to the HR Office are handled in a professional, welcoming and friendly manner. IR Industrial RelationsDraft the annual IR Plan which will form part of the GFC Annual HR Plan.Facilitate end-to-end disciplinary processes in liaison with line management.Where required, offer support to the Group Legal Advisor at the Bargaining Council/ CCMA with respect to GFC cases.Provide responsive and high-quality support, training and advice to all parts of the business including line managers.Together with the HR Manager, ensure the appropriate management of all employee relations issues including grievances, poor performance and disciplinary action.Assis
See product

Delmas (Mpumalanga)
Astral is a leading South African integrated poultry producer and has the following vacancy- Millwright · Maintaining property, plant and equipment in a safe and acceptable overall condition; · Maintenance (mechanical and electrical) of all boiler equipment as required; · Maintenance (mechanical and electrical) of all Feed Mill Machinery as required; · Testing of all safety features and mechanisms; · Fault finding and improvements; · New installations and modifications; · Attend to breakdowns with urgency; · Journeyman to apprentices; · Root cause failure analysis reports; · Adhere to all company policies and procedures; · Participate in the 20 keys improvement system; · Complete internal statutory inspection as requirement; · General housekeeping as required; · Stock take as required; · Meet all requirements for maintaining Quality system accreditation. · Qualified and Trade Tested as Millwright with minimum N2 qualification · 5 years post trade test experience in the manufacturing industry; · Feed Mill experience preferable will be an advantage; · Knowledge and experience of PLC, and VSD Systems; · Ability to lead a team and achieve maintenance KPI’s; · May be required to work shifts and public holidays; · Standby and call out duties; · Motor vehicle licence and own reliable transport; · Willing to reside in Delmas(must respond to call outs within 30 minutes) · Qualified and Trade Tested as Millwright with minimum N2 qualification · 5 years post trade test experience in the manufacturing industry; · Feed Mill experience preferable will be an advantage; · Knowledge and experience of PLC, and VSD Systems; · Ability to lead a team and achieve maintenance KPI’s; · May be required to work shifts and public holidays; · Standby and call out duties; · Motor vehicle licence and own reliable transport; · Willing to reside in Delmas(must respond to call outs within 30 minutes)
See product

East London (Eastern Cape)
Automotive - Logistics Manager Top Automotive Supplier seeking a Senior Logistics Manager for their East London plant. Responsibilities, but not limited to:Strategy and Development - Contribute to the creation and implementation of best practice logistics vision, strategy, policies, processes and procedures to aid and improve operational performancePlan, manage and evaluate logistics operations liaising with internal stakeholders, suppliers, logistics providers, transportation companies and customersFinancial Budget and Control - Hold responsibility for department budgetDeliver solutions to logistics problems while maintaining high levels of quality and service within budgetary requirementsPeople Management - Manage, coach and develop a high performing team that meets agreed objectives and delivers best practice results, added value and continuous improvementsRequirements:Relevant Degree in Logistics or Supply Chain ManagementMinimum of 10 year’s experience in a Logistics Management role within the automotive manufacturing industrySolid knowledge of JIT, KANBAN Strong IT systems knowledge and skills including knowledge and understanding of specialist systems such as Enterprise Resource Planning (ERP), Bill of Material (BOM) and customer data systemsAdvanced Excel userAbility to analyse and manipulate technical and complex data and provide meaningful informationinclude certification in dangerous goods handling and aviation securityStrong knowledge and understanding of a variety of manufacturing and automotive processes and components and of supply chain managementPlease forward CV and ALL supporting documentation to, recruiter1@profilepersonnel.co.za"(recruiter1@profilepersonnel.co.zaShould you not hear from Profile Personnel within 14 days please consider your application unsuccessful for the vacancy. Please note all applications will automatically be added to our database for future vacancies.
See product

Uitenhage (Eastern Cape)
Our client in the automotive sector seeks to employ a Production Supervisor to be based at their plant in Uitenhage. Duties: Production Planning Co-coordinating all activities of the department including shifts Ordering and ensuring raw materials conform to process requirements Ensure machines are utilized efficiently in order to meet set targets Check quality and record and report deviations (ISO TS 16949) Ensure all health, safety and environmental standards are maintained Plan machine maintenance downtime in consultation with Maintenance Conduct training and appraising of employees Ensure all departmental budgets are met Control material utilization and minimize waste Provide good customer service and communication Promote good employee relations Complete daily reports accurately and on time Deal with daily industrial relation problems Ensure all manufacturing systems are maintained Ensure the factory is opened and closed daily Carry out monthly stock takes Apply & enforce principles Requirements: National Diploma or other relevant qualification Minimum 3 years’ experience in manufacturing environment Good technical product and process knowledge Strong communication skills in the English language Ability to plan, organize and control Ability to motivate a workforce Ability to work as a team player Ability to work with minimal supervision Self-disciplined Good communicator Honest, punctual and reliable Job Reference #: PE004317/CT
See product

Pretoria (Gauteng)
HPK Innovate is an industrial engineering consulting company specializing in services for businesses in the automotive, currency, chemical, warehousing and the food and beverage manufacturing sectors. With twenty years of experience, we have gained the expertise needed to make your business vision come to life. We have successfully completed many projects and left our customers satisfied, so we feel confident that we can help your project succeed. Services include: Engineering Support, Preventative Maintenance, Process Design, Specialized Training, Project Management, Industrial Engineering Consulting, Manufacturing Process Improvement, Plant Design, Specialized Shop Floor Improvement, Warehouse design and improvement, Equipment Maintenance. Visit https://hpkinnovate.com for a full list of the services we offer or get in touch via 0824538225 to find out how we can assist you with your projects based in the Greater Johannesburg and Pretoria areas.
See product
-
Next →